- More than 1 billion car tires reach the end of their life each year, and dealing with the resulting waste is an escalating management headache the world over.
- But long before tires are thrown away, they leave behind a trail of environmental harm stretching from tropical forests, along supply chains, and to consumers. Limited rubber traceability risks deforestation, experts warn, while other research shows that tire wear releases potentially toxic microplastic pollution.
- It needn’t be this way: Circular economy solutions — reducing, reusing and recycling materials in closed loops — could offer tire pollution solutions. However, these solutions come with limitations and trade-offs.
- A tire redesign is greatly needed to increase longevity, as is the cultivation of new sources of deforestation-free rubber, and alternative end-of-life strategies that emphasis recycling of the dozens of components found in tires. But given the complex makeup of today’s tires, there won’t be one simple solution.
Imagine a heap of a billion vehicle tires towering overhead, the total number humanity throws away in just one year — worn-out tires tossed into landfills, burned, or littering the landscape.
While that’s a visually distressing image, the harm tires do starts where they’re sourced, with current and future car fleets leaving an environmental trail stretching from tropical rainforests to rubber plantations to global roadsides, along waterways, and even into the atmosphere — impacting global biodiversity and human health.
Experts say that applying a circular economy model to tire production and disposal could limit massive resource demand, while simultaneously turning this globally vexing waste stream back into valuable materials.
But no matter the solution, the complex composition of the average tire — containing more than 400 chemicals and compounds — means there’s no single silver-bullet solution to this persistent problem.
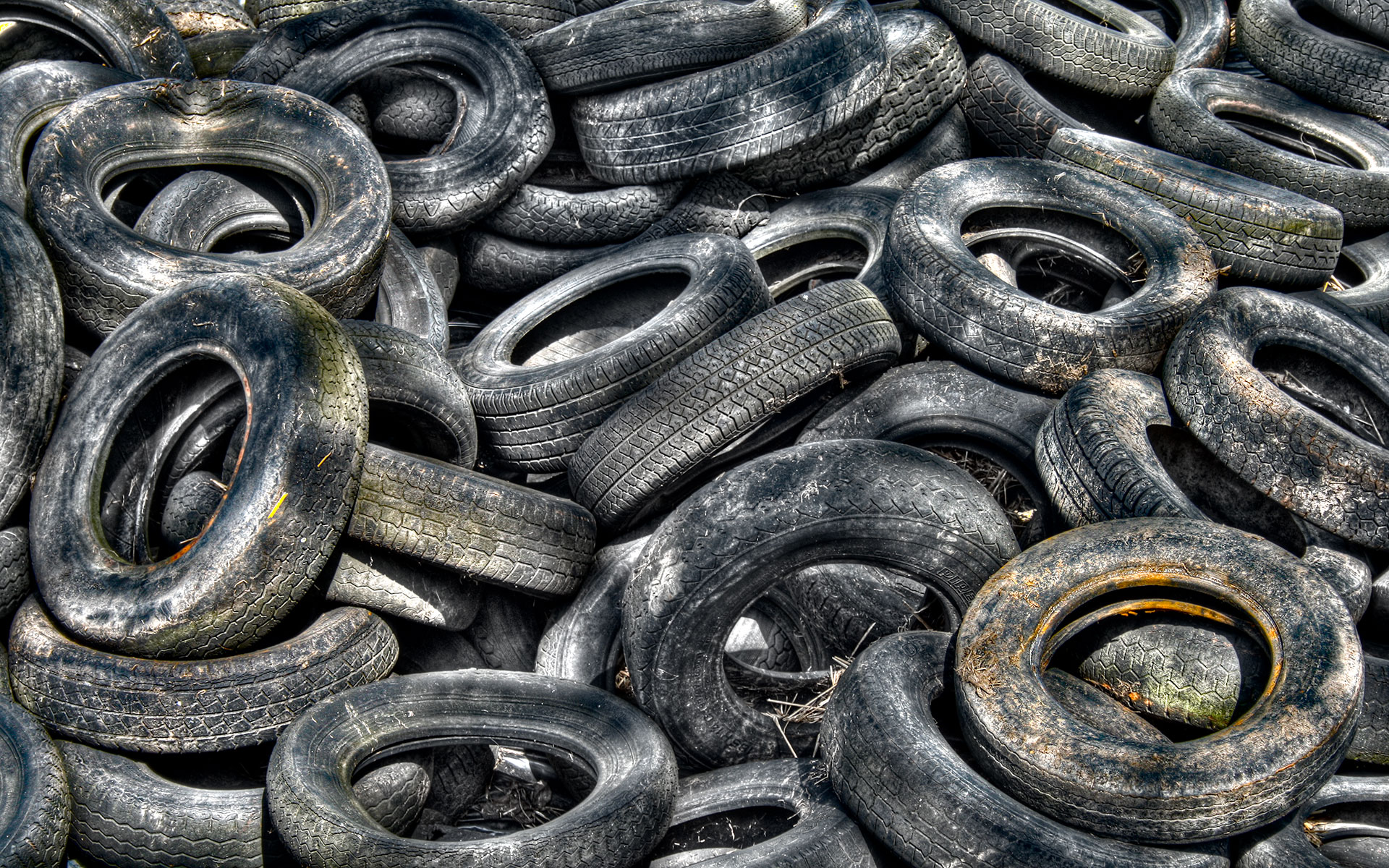
A toxic conundrum
Tires typically start their life’s journey in the tropics, with rubber produced predominantly by smallholder farmers on monocrop plantations. Current production methods risk ongoing deforestation and harm to biodiversity, along with uncertain livelihoods for farmers. Some 70% of the world’s natural rubber ends up in car tires with most coming from tropical countries such as Thailand, Indonesia and Malaysia.
But natural rubber is just one component found in a modern tire. Like the cars they’re fitted to, tires are composite products, made of steel and hundreds of chemicals and compounds that give them durability and strength.
Unpacking tire environmental impacts is complicated, say experts, partly due to that complexity, and also due to the lack of publicly available data on tire ingredients.
What is known is that tire impacts are spread far and wide: Rolling on roads wears them down, releasing microplastic particulates everywhere — making them one of the most common pollutants in Earth’s oceans today, according to research.
“We know enough to say that it is possibly the biggest, and possibly the least well understood, environmental problem related to transportation,” says Nick Molden, CEO of Emissions Analytics, a company that conducts research into tire wear.
Some tire waste kills. A tire additive known as 6PPD, for example, has been identified as particularly alarming. The mass die-off of coho salmon in the U.S. Pacific Northwest has been linked to tire wear via chemical pollution in the form of this antioxidant.
As it protects tires, 6PPD transforms into 6PPD-quinone, a highly toxic chemical. Edward Kolodziej, who led the team that made the discovery and a researcher at the University of Washington Tacoma, describes 6PPD-quinone as possibly one of the most toxic substances known to aquatic species.
Since its discovery, researchers have found 6PPD and 6PPD-quinone in fresh- and saltwater, ocean sediments, air, soil, and human urine; yet its overall ecological and health impacts remain unknown. Many other tire chemicals lack sufficient study as to risk.
Chemical-laden tires at the end of their life pose a serious waste management headache. Landfilling them is no solution; no matter where they’re dumped, heaps of aging tires become a pollution source as they break down, leaching toxins into soils and aquifers. Burning tires, another common practice, merely transfers that toxic burden from soils and waters to the sky. Research shows that open burning can emit carbon monoxide, nitrogen dioxide, sulfur dioxide, particulate matter, and other compounds at potentially harmful levels, posing a risk to human health.
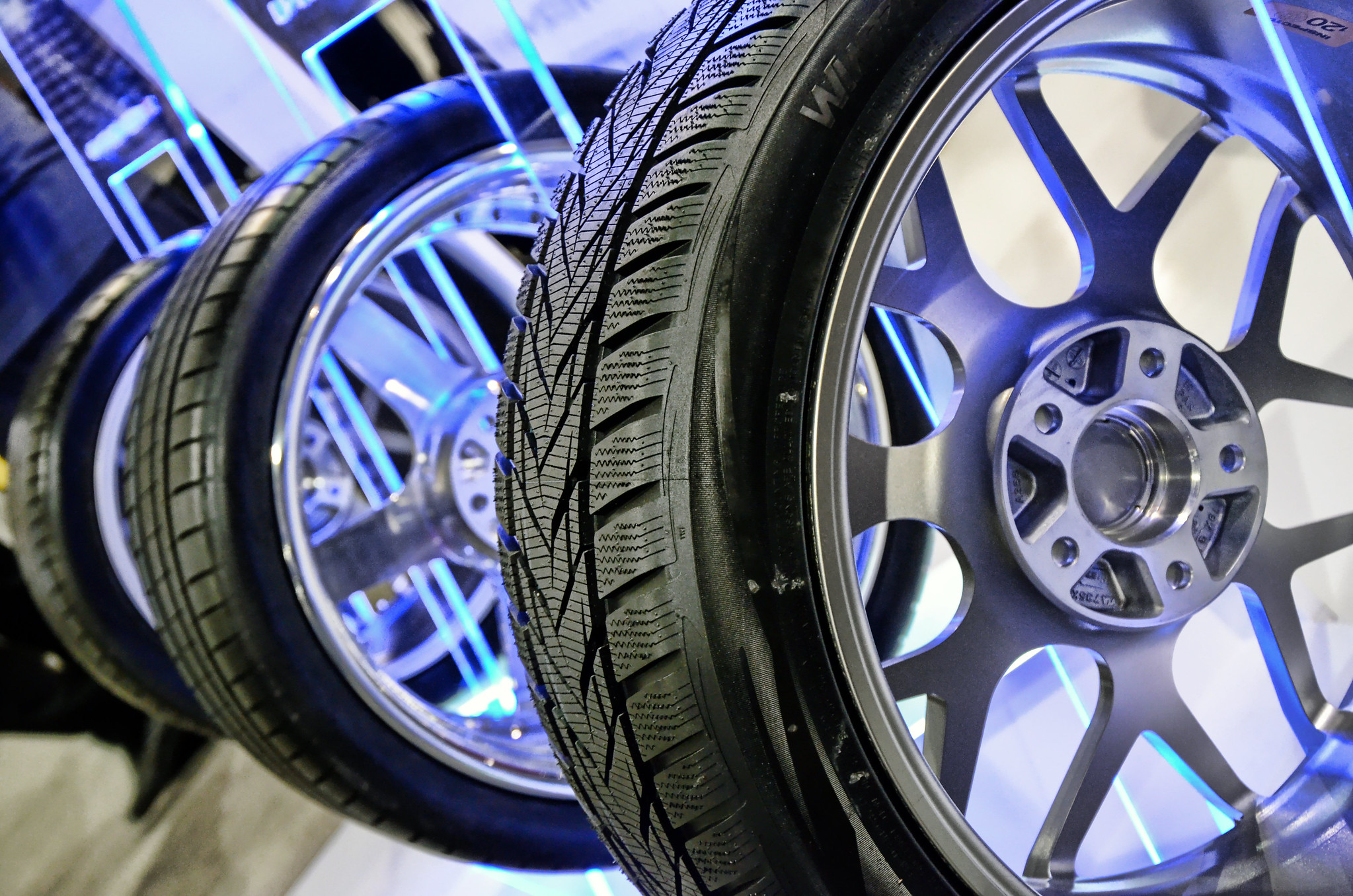
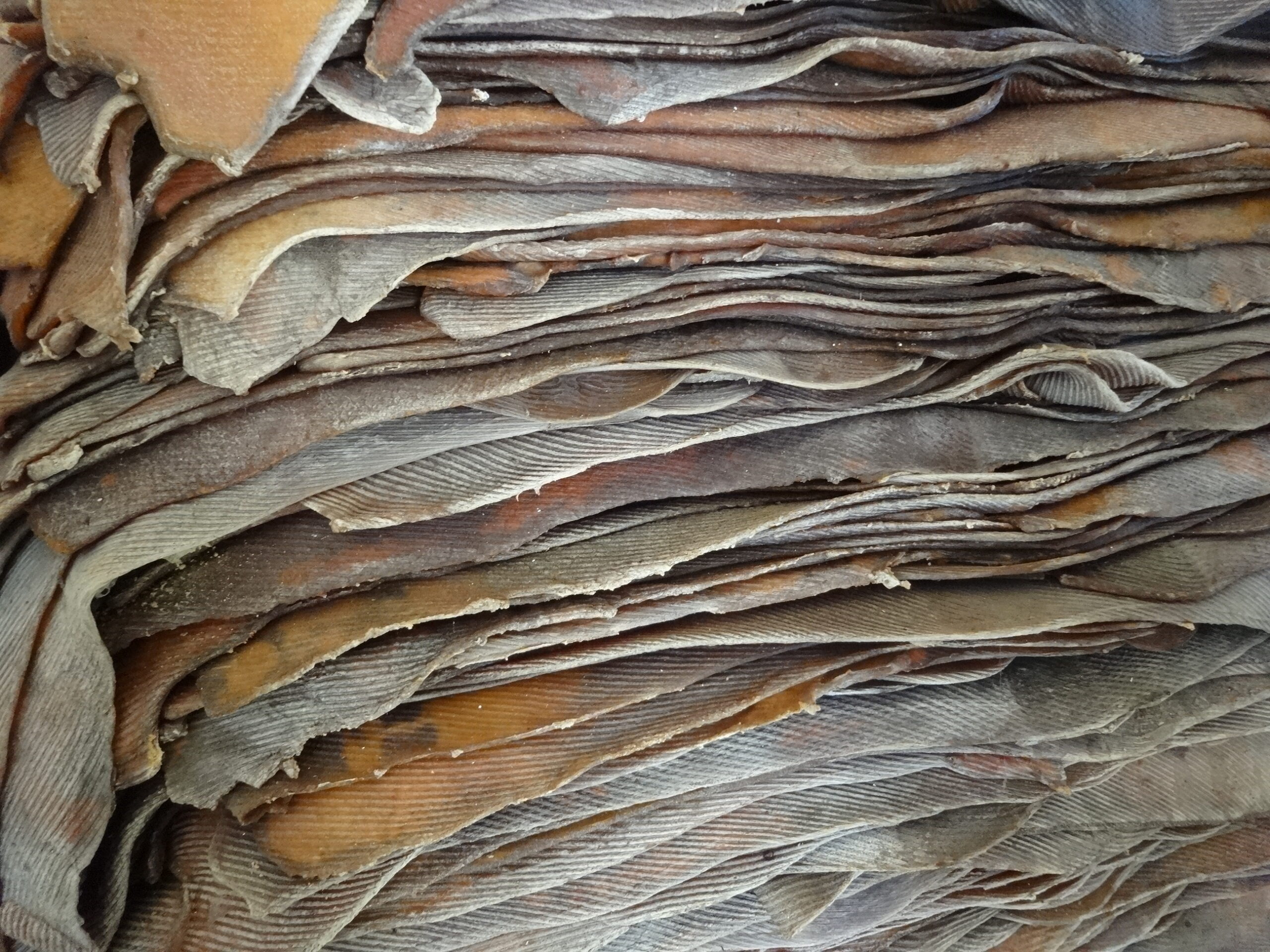
Circling the tire economy
At its core, the circular economy seeks to reduce, reuse and recycle materials in closed loops, with zero waste as the ultimate goal. Tires are prime circularity candidates, say analysts, because when discarded they retain a wealth of useful materials. But getting at those materials, processing them, and making a profit doing so is a major challenge.
“Successful ELT [end-of-life tire] management systems … foster circular flows of materials … and avoid the unregulated dumping of tires,” says Gavin Whitmore, senior communications manager at the Tire Industry Project (TIP), a group that includes some of the world’s major tire manufacturers.
But ELT recovery is woefully inadequate today. A 2019 TIP report noted that in 45 countries surveyed, just 42% of end-of-life tires were used in material recovery and 15% in energy recovery. Some common management options include shredding tires into small rubber pellets for use as construction filler, in rubber-modified asphalt, or in artificial sports pitches.
Millions of waste tires become alternative energy, dubbed tire-derived fuel, burned in kilns for the production of cement, steel, pulp and paper. This market is only set to grow in coming years, say analysts, due to its low cost and reported reduced carbon emissions. Some argue that tire-derived fuel could even lessen the heavy environmental footprint of the cement and paper industries, while helping dispose of tire waste.
TIP notes that “energy recovery can be a particularly efficient way to deal with high volumes of ELT and eliminate long-standing stockpiles because it is generally technically straightforward to implement” while “the use of ELT as an alternative fuel is also encouraged to reduce CO2 emissions.”
But some experts argue that these common disposal routes — grinding down tires or burning them — amount to little more than downcycling, failing to maximize the full potential for material reuse of waste tires.
Not surprisingly, some of these trumpeted solutions are also plagued by their own environmental issues.
Researchers in Ireland, for example, found that the spreading of rubber crumb on artificial sports pitches is a source of microplastics and may pose health concerns due to the toxic chemicals locked up in the materials. The European Union is aiming to ban this widespread practice, potentially leaving a backlog of tires to be disposed of properly.
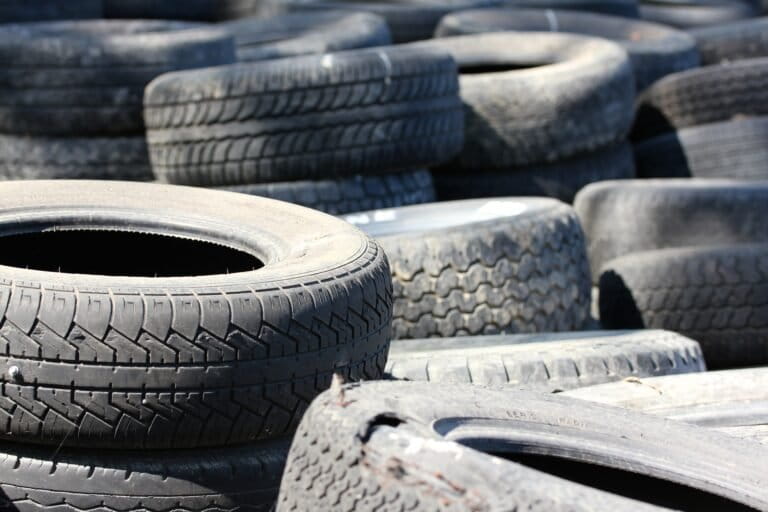
Making old tires new again: Reusing and recycling
Two other solutions tipped to deal with tire waste on a large scale offer the promise of circularity: devulcanization and pyrolysis, both of which could ultimately make new tires out of old, according to analysts.
“The most important part of the circular economy for tires is getting the original product back into its intended application,” says Jon Visaisouk, chief operating officer of Tyromer. His company produces devulcanized rubber from used tires, which can replace some raw materials in new tire production. Currently, the firm can process between 100,000 and 150,000 waste tires per year, he says.
Devulcanization is a promising low-energy solution for dealing with tires en masse, but has its limitations from a circularity perspective, according to Niles Beadman, a patent attorney with Mewburn Ellis: “You can’t use that devulcanized product as 100% raw material. You would still typically mix it in with some virgin raw material,” he explains, claiming that pyrolysis shows more promise.
Pyrolysis works by heating tires in the absence of air to break them down. This turns waste tires into separate reusable materials such as recovered carbon black for new tires, oils that can be upgraded to alternatives to diesel, and gases to loop back in and power the whole system, reducing its energy intensity. Prior to the pyrolysis process, the tire’s steel is stripped for reuse. Pyrolysis is often referred to by advocates as “environmentally safe” and a vital tire waste solution.
“What we’re bringing to the table is a solution that is not only environmentally friendly, but can work at scale to actually make a dent in the problem,” says Vianney Vales, CEO of Wastefront in Norway, which uses pyrolysis.
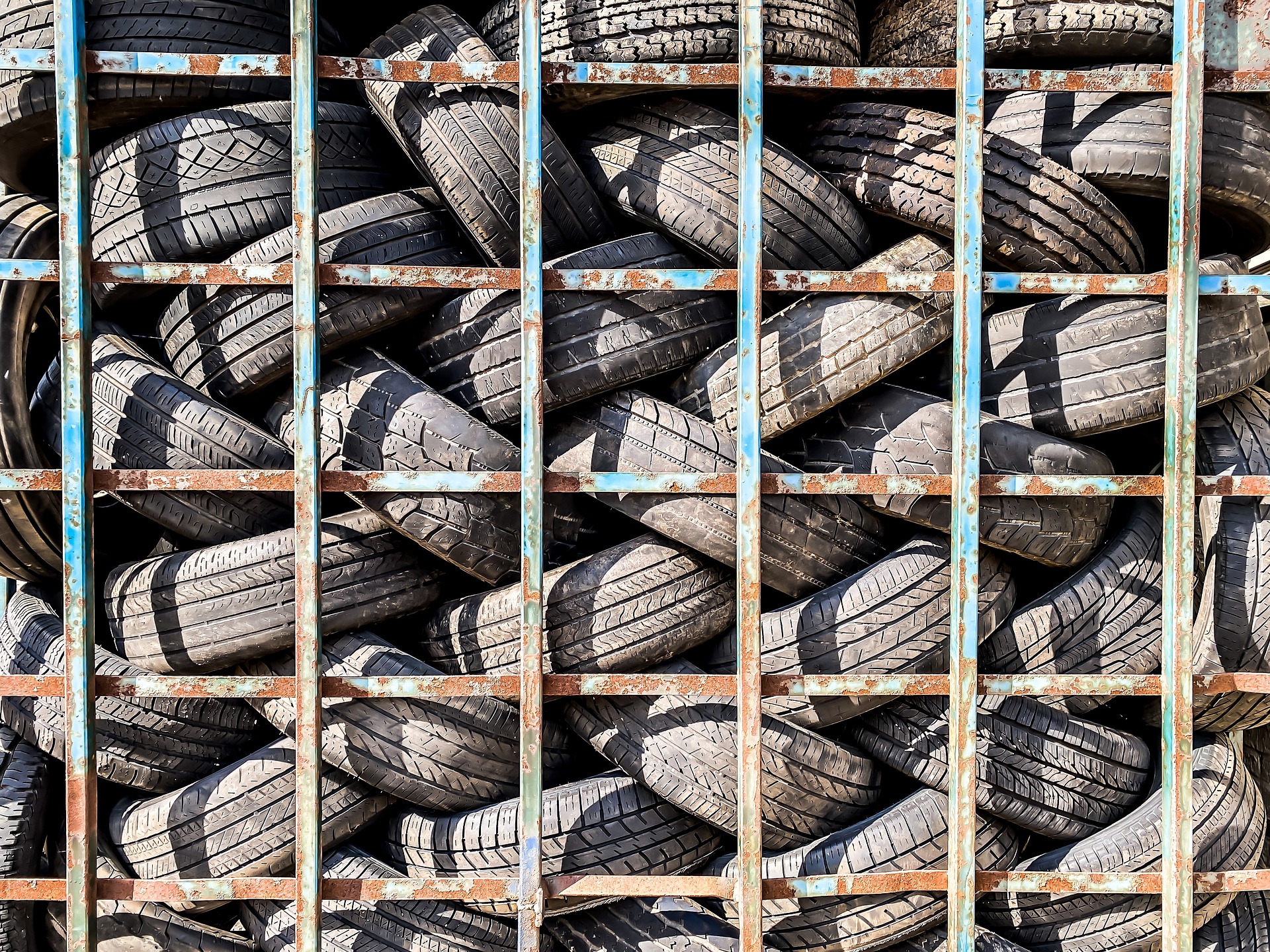
But to break tires down into those useful products, the energy-intensive pyrolysis process creates multiple waste streams, is linked to significant air and water pollution, and produces carbon emissions. Pakistan banned the use of pyrolysis units last year due to toxic pollution concerns.
One frequent problem with pyrolysis is the quality of products made by the process, says Dina Czajczyńska, a researcher at Wrocław University of Science and Technology in Poland. Another “really important environmental issue” is highly toxic sulfur emissions — meaning that, without desulfurization of emissions and of the products themselves, pyrolysis can be environmentally harmful, she says.
“What we are trying to do is solve this [tire] problem without having an impact on the environment around us,” says Thomas Sörensson, CEO of Scandinavian Enviro Systems, a Sweden-based company that employs pyrolysis. “We use the latest technology for reducing emissions, taking care of sulfur, and have put in place a system that is meeting the highest environmental regulations.”
Practiced conscientiously, pyrolysis may have the potential to convert massive amounts of tires into renewable products, say some experts. A Wastefront facility under construction in northern England could absorb about 20% of the U.K.’s annual waste tire output once it goes live in 2024, according to Vales.
But as other experts underscore, the environmental footprint of widespread pyrolysis use as a tire solution could be large if not appropriately managed and regulated.
“This is going to be a crucial part of the circular economy for cars and plastics more generally. How can we extract value and recycle these millions of waste tires?” asks Molden, who notes that while pyrolysis offers a “major opportunity” for tire recycling, “you have to [power] it with green energy, and you have to make sure you don’t create all sorts of toxic waste that has to be dumped somewhere in the process.”
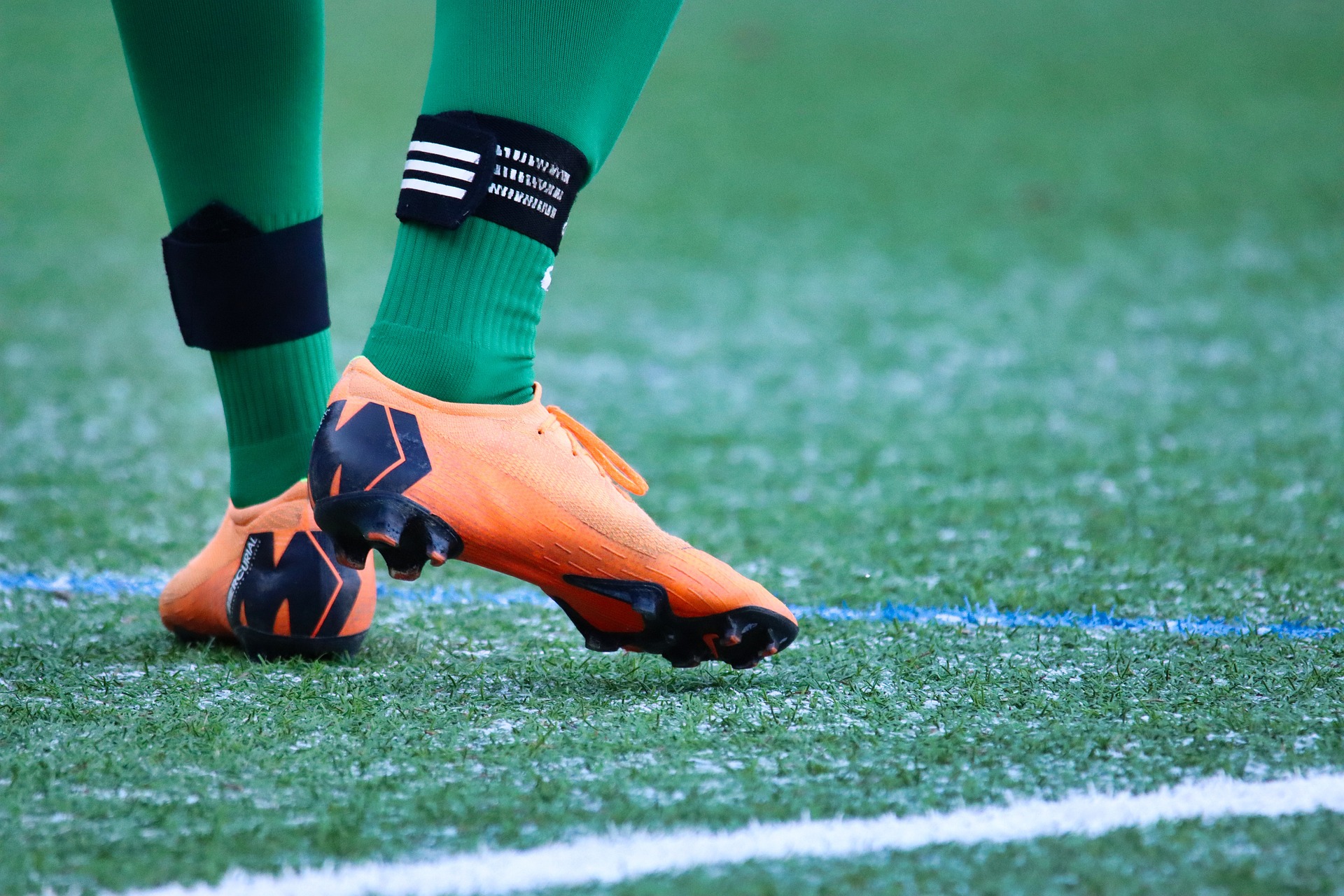
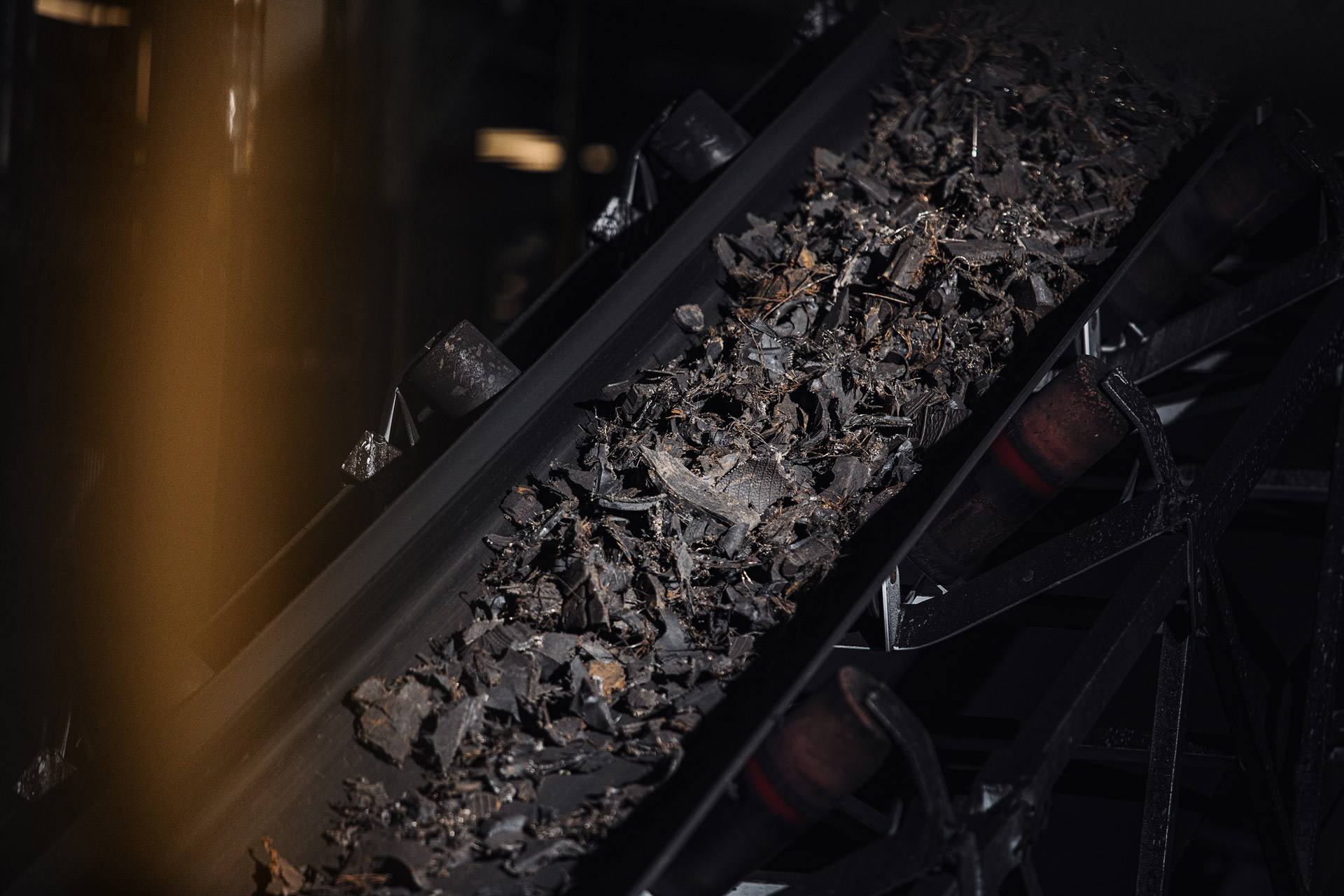
Circular rubber sources
Dealing with mountains of end-of-life tires is only part of the sustainability challenge facing the tire industry and the automotive sector at large. A recent report by the Zoological Society of London (ZSL) underlines the lack of transparency in rubber supply chains, risking unseen links to deforestation and wider biodiversity harm.
Given that the projected demand for tires is set to increase year-on-year, unabated by the switch to electric vehicles, more rubber will be required, which may put tropical forests deeper in harm’s way.
To this end, tire manufacturers are investigating alternative natural rubbers, such as Russian dandelion, from which limited quantities of tires are already made. These innovative sources could serve as substitutes to tropically-sourced rubber.
“The major problem that we’re facing is higher demand for natural rubber in the next few years,” says Dirk Prüfer, a professor of plant biotechnology at the University of Münster in Germany whose work focuses on producing rubber from Russian dandelion.
He says alternative rubbers could supply at least some of future demand, without endangering biodiversity-rich areas and tropical forests. The Russian dandelion, for example, can grow on so-called marginal lands, and doesn’t compete with food crops, he says.
However, ZSL sustainable business specialist Sam Ginger says he doubts the efficacy of this solution. “It would be a big distraction to try and start establishing huge plantations of dandelion without solving the [sustainability] issues that [already exist] within the rubber supply chain,” he says. That new source would distract from the problems faced by the “6 million smallholder farmers that are currently dependent on this industry.”
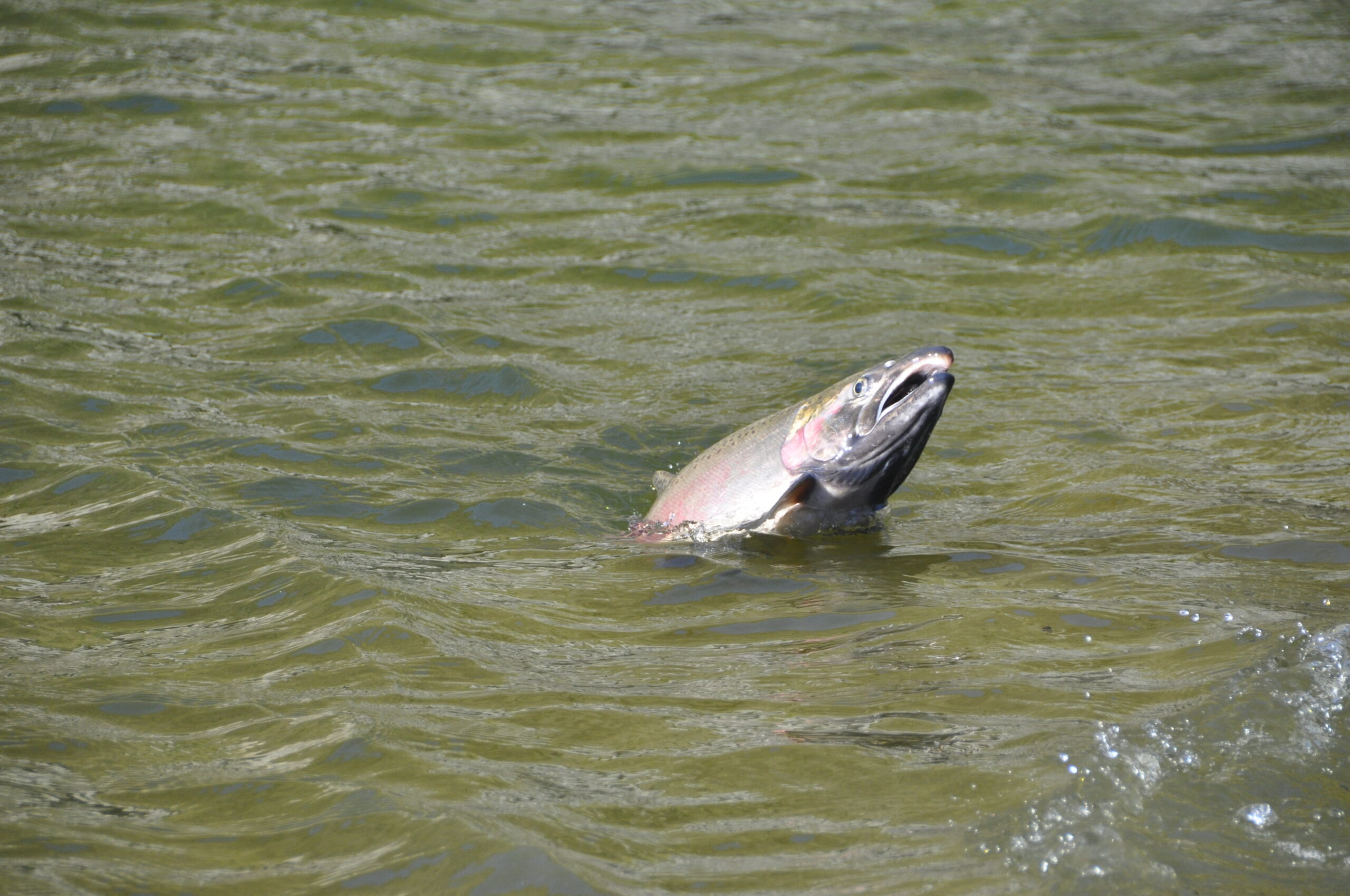
Experts also underline the need for increased regenerative agricultural practices if supply chain circularity is to be achieved. Ginger says the natural rubber industry already offers multiple opportunities in this space, working with farmers to put regenerative and agroforestry practices in place to support both biodiversity and farmers’ livelihoods.
Stefano Savi, director of the Global Platform for Sustainable Natural Rubber, says that fundamentally “we need to change the [tire production] system so that the farmers become entrepreneurs.”
“Today, most of the farmers are extractors of these commodities and deplete natural resources because they’re not geared towards [sustainably] managing the land,” he notes. Like Ginger, he says that by helping smallholders apply circular principles, including pesticide reduction and better water management, then “you will be able to do more with less. You will be able to have a better system.”
But such changes are all predicated on fully tracing and creating transparency in supply chains, and will require wider collaborations from industries such as car manufacturers. Ginger adds: “To make a truly transformative effort across the whole supply chain, you need to have carmakers involved. They need to be contributing funds to any sort of sustainability effort across the whole supply chain, all the way down to the smallholders.”
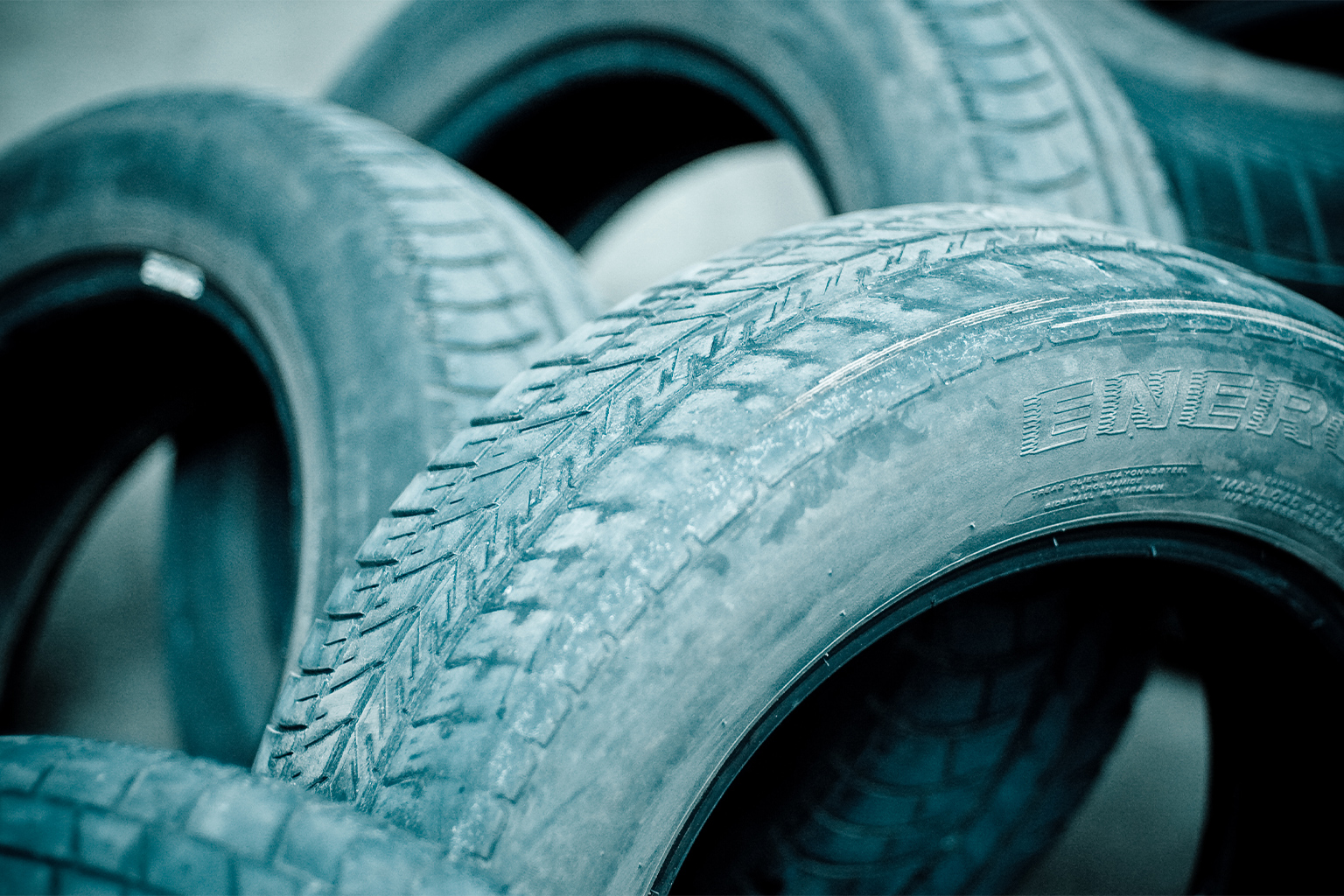
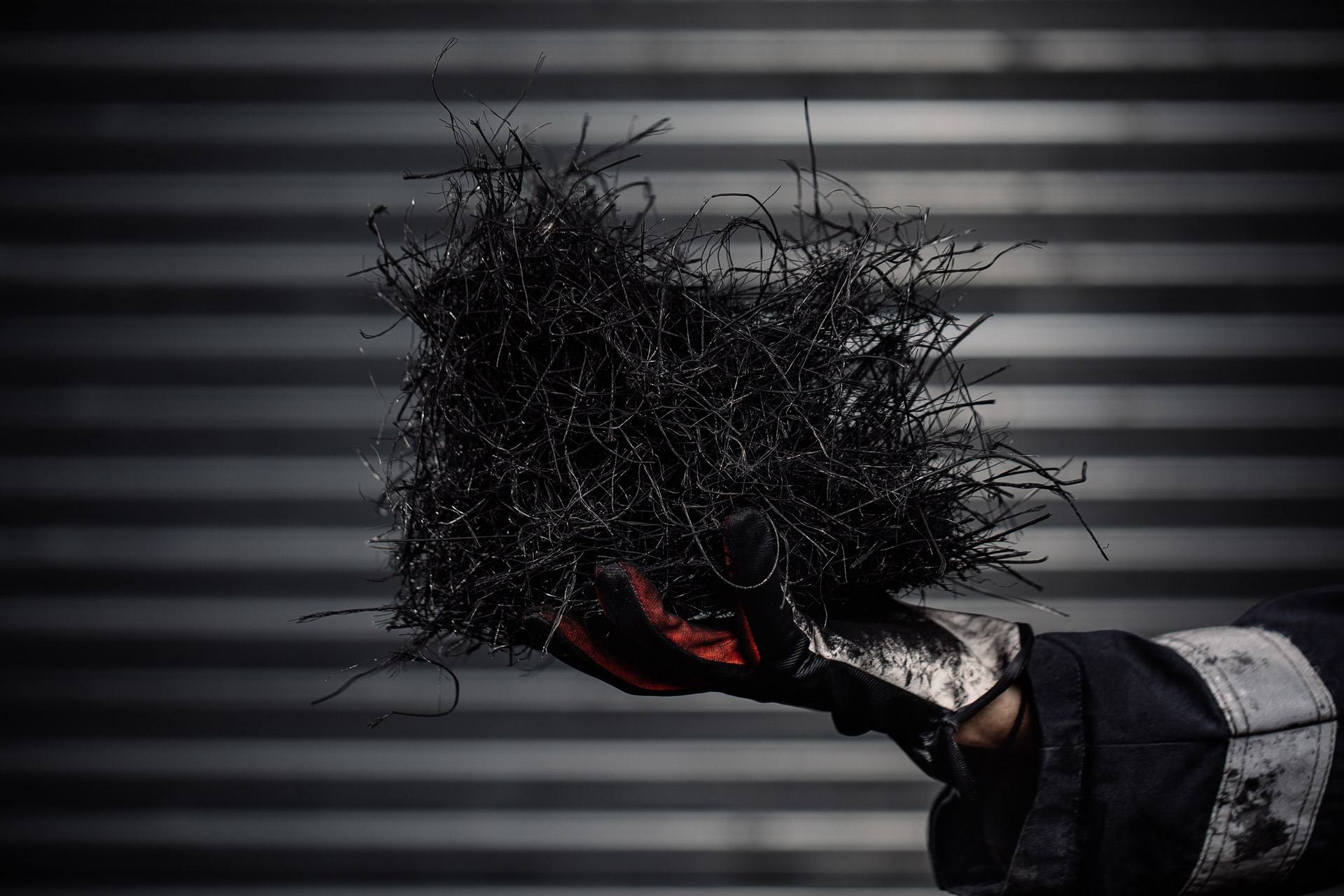
Achieving circularity and ‘using less cars’
Tires are just one component of the wider circularity challenges facing the auto industry. But tires represent a fast-growing, thorny problem, as vehicle use worldwide increases material demand.
Tire wear, too, is predicted to get worse as EVs become more prevalent, in part due to their bulkier weight, likely exacerbating associated microplastic and chemical pollution from problematic tire components. Solutions are urgently needed now, researchers say.
Kolodziej especially emphasizes the need to find a safe alternative to 6PPD, which should be a priority for the industry. “I think there’s still a lot of discussion around what should be evaluated in that chemical screening process to develop the circular economy” in order to “reuse, remanufacture and recycle things like tires.”
But not all experts are convinced that a materially focused vision of circularity, and particularly recycling, will be enough to reduce tire-associated environmental problems.
Czajczyńska, for example, emphasizes the need to reduce overall consumption: “We have to think about using less cars, using more bicycles and public transportation to avoid the problem of [tire] waste,” she says. “Because no matter how well you process or treat waste tires, [they] will always produce some emissions or another waste product.”
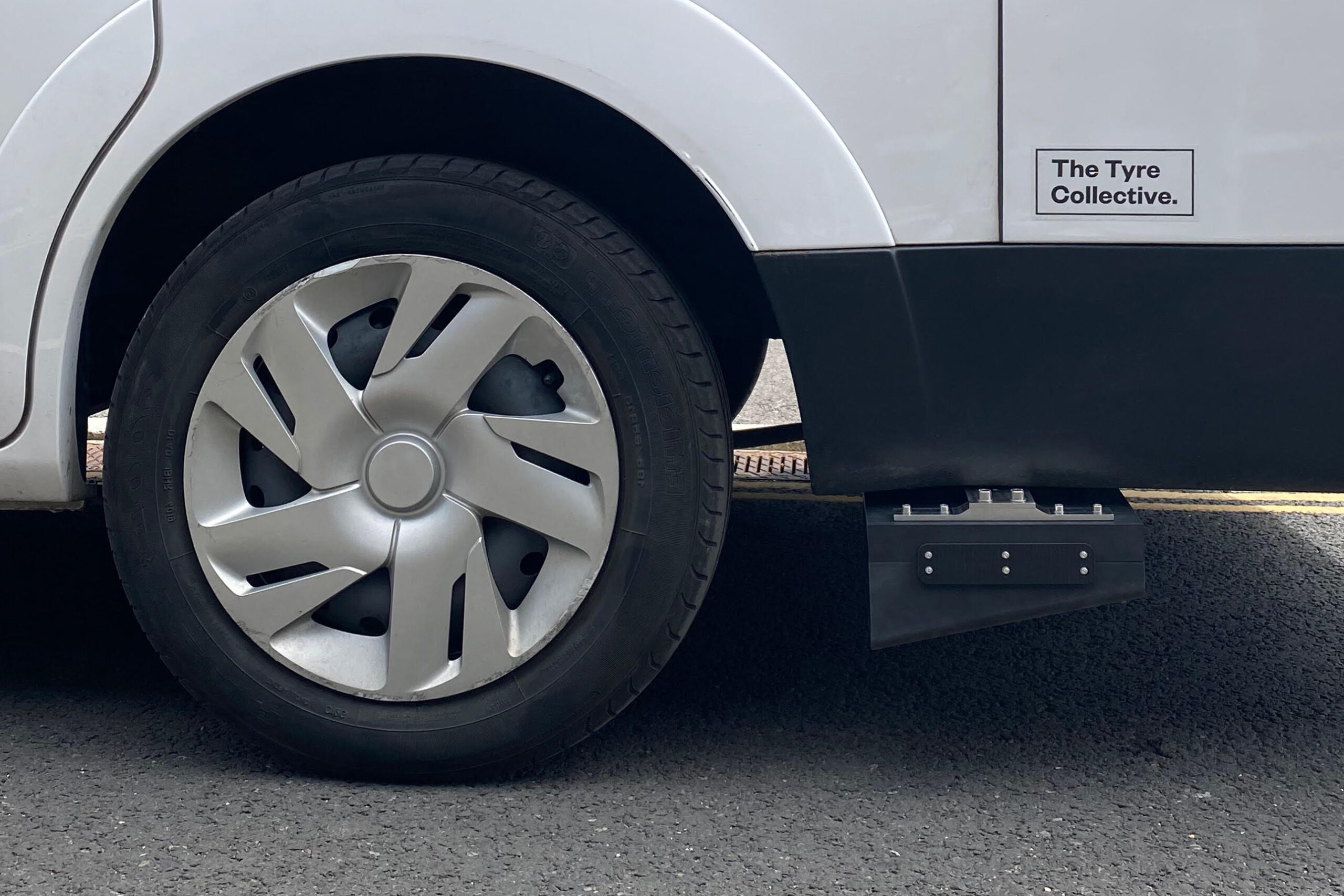
Kaustubh Thapa, a researcher at Utrecht University in the Netherlands, agrees that a “better solution” would be to offer alternatives that reduce the need for ever more tire production now and in the future.
“I think that when the circular economy is very technocratic and material-focused, it just shifts some problems to other parts,” he says. “If we want to fix these challenges in a systematic way, then we need to also include the social dimension in the circular economy.”
Banner image: Increasing tire longevity, repairing and reusing component parts, are all tire circular solutions. A plant in Spain, operated by Life for Tyres Group and funded by the European Union, aims to recover materials (such as carbon black) and produce synthetic fuels (including biogas) from 26 million metric tons of end-of-life tires each year, equivalent to around 9% of Spain’s annual use. Image by Egor Myznik via Unsplash (Public domain).
FEEDBACK: Use this form to send a message to the author of this post. If you want to post a public comment, you can do that at the bottom of the page.
The circular economy: Sustainable solutions to solve planetary overshoot?
Citations:
Tian, Z., Zhao, H., Peter, K. T., Gonzalez, M., Wetzel, J., Wu, C., … Kolodziej, E. P. (2021). A ubiquitous tire rubber-derived chemical induces acute mortality in coho salmon. Science, 371(6525), 185-189. doi:10.1126/science.abd6951
Johannessen, C., Saini, A., Zhang, X., & Harner, T. (2022). Air monitoring of tire-derived chemicals in global megacities using passive samplers. Environmental Pollution, 314, 120206. doi:10.1016/j.envpol.2022.120206
Cao, G., Wang, W., Zhang, J., Wu, P., Zhao, X., Yang, Z., … Cai, Z. (2022). New evidence of rubber-derived quinones in water, air, and soil. Environmental Science & Technology, 56(7), 4142-4150. doi:10.1021/acs.est.1c07376
Du, B., Liang, B., Li, Y., Shen, M., Liu, L., & Zeng, L. (2022). First report on the occurrence of N-(1,3-Dimethylbutyl)-N′-phenyl-p-phenylenediamine (6PPD) and 6PPD-quinone as pervasive pollutants in human urine from South China. Environmental Science & Technology Letters, 9(12), 1056-1062. doi:10.1021/acs.estlett.2c00821
Jimoda, L. A., Sulaymon, I. D., Alade, A. O., & Adebayo, G. A. (2017). Assessment of environmental impact of open burning of scrap tyres on ambient air quality. International Journal of Environmental Science and Technology, 15(6), 1323-1330. doi:10.1007/s13762-017-1498-5
Shakya, P. R., Shrestha, P., Tamrakar, C. S., & Bhattarai, P. K. (2008). Studies on potential emission of hazardous gases due to uncontrolled open-air burning of waste vehicle tyres and their possible impacts on the environment. Atmospheric Environment, 42(26), 6555-6559. doi:10.1016/j.atmosenv.2008.04.013
Nadal, M., Rovira, J., Díaz-Ferrero, J., Schuhmacher, M., & Domingo, J. L. (2016). Human exposure to environmental pollutants after a tire landfill fire in Spain: Health risks. Environment International, 97, 37-44. doi:10.1016/j.envint.2016.10.016
Yasar, A., Rana, S., Moniruzzaman, M., Nazar, M., Tabinda, A. B., Haider, R., … Ullah, S. (2021). Quality and environmental impacts of oil production through pyrolysis of waste tyres. Environmental Technology & Innovation, 23, 101565. doi:10.1016/j.eti.2021.101565
Campbell-Johnston, K., Calisto Friant, M., Thapa, K., Lakerveld, D., & Vermeulen, W. J. (2020). How circular is your tyre: Experiences with extended producer responsibility from a circular economy perspective. Journal of Cleaner Production, 270, 122042. doi:10.1016/j.jclepro.2020.122042